Used when creating a Butt Weld between two sections of train rail, this shear takes a lot of abuse. At the same time, it must follow very tight tolerances to maintain the profile of the rail (especially when a high speed train is running across it).
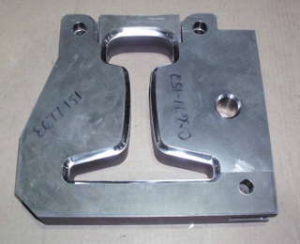
A butt weld is created in the field using a mobile electric flash-butt welder. The two sections are joined and electricity is applied to the rail ends. The flash-butt welder squeezes the sections together at very high pressure, permanently joining them, but this also creates a seam at the joint with a segment of slag.
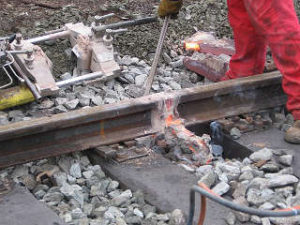
(notice the manual shear in the background)
“Thermite Rail Welding” by PetrS. 2013 licensed under CC
The RAIL WELDING SHEAR is clamped onto the rail and slid along the rail, by the mobile welder, cutting off the hot slag leaving only a small remainder that will be later ground smooth.
These shears are precision cut out of Nitronic 60 – a high strength metal known for it’s wear resistance – with a wire EDM machine. The EDM unit cuts parts slower, but with more precision than a waterjet or laser cutter.
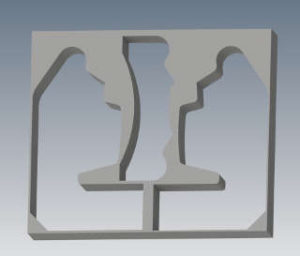
The final grooves are added via a CNC and the units are then inspected. A hard-surface weld is added and machined to create a precision cutting edge. The parts are assembled to complete the rail welding shear.
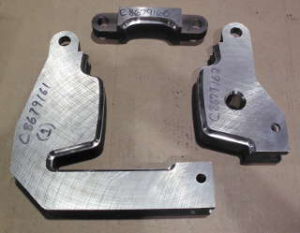
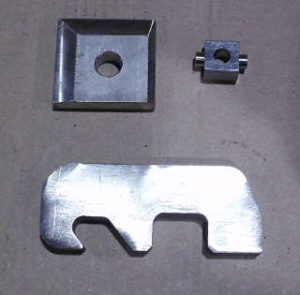
These are ready for the rail and making the travels of passengers and goods go smoother and safer.
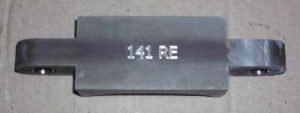
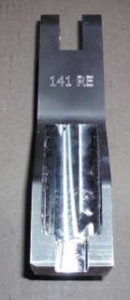
This video shows a portable flash-butt welder in use. Notice the Rail Shear clamped on the rail before the unit is lowered on the section.
Riggs Machine & Fabricating – Serving industry in KY, OH and WV for over 45 years!